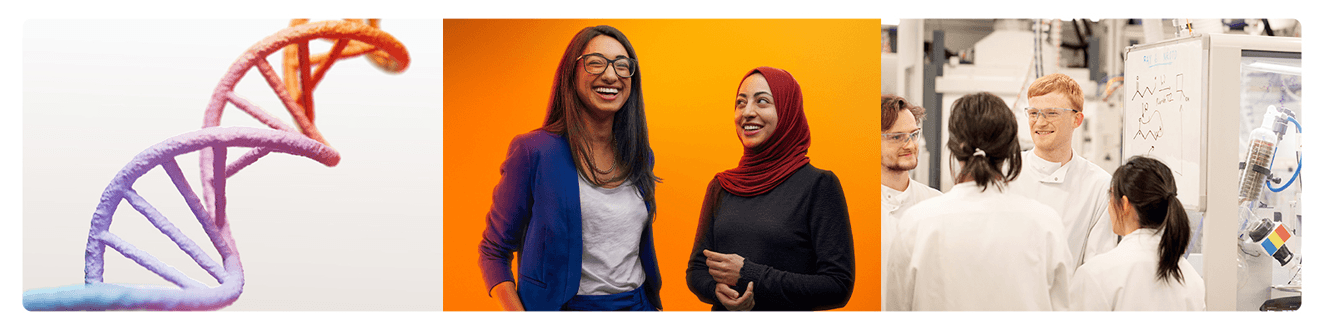
Rating
- 1. Please give an overview of your role and what this involves on a day-to-day basis:
- 2. Have you learnt any new skills or developed existing skills?
- 3. To what extent do you enjoy your programme?
- 4. How valued do you feel by GSK?
- 5. How well organised/structured is your programme?
- 6a. How much support do you receive from your training provider?
- 6b. How much support do you receive from your employer?
- 7. How well does your salary/package meet your costs?
- 8. Are there many opportunities outside of work?
- 9. Would you recommend GSK to a friend?
- 9b. Why?
- 10. What tips or advice would you give to others applying to GSK?
Job title: Engineering Apprentice Daily tasks: routine work, including machine maintenance, calibrations, plant maintenance. Fixing breakdowns and other issues with machinery or plant. Being involved in new installations. Daily interactions internal: mostly with fully qualified technicians and some other engineering apprentices, first line leaders, shift managers and ops managers. Daily interactions external: very rarely interact with people off site. Responsibilities: Complying to safety policies, code of conduct, college work and general stuff like timekeeping ect. I have no responsibilities that involve technician work as I am not qualified. My greatest responsibility in this regard is to learn! Day-to-day: Most days I am working with technicians, either helping them with their work or shadowing what they're doing. I am given jobs to do but they are supervised by qualified technicians. Other than that, I have day release to college once a week.
Qualifications (all gained externally): I have gained a level 3 qualification in engineering, tow level 3 PEOs (competency) in electrical engineering and instrumentation, passed my 17th edition qualification (electrical domestic), safety qualifications, I am currently working towards a level 4 in mechatronics. Internal training courses: only site safety courses such as fire training and code of conduct - not recognised by another body. Professional skills: where do I even start! skills were always there, but coupled with new knowledge and practice they have improved 1000 fold. What have a learnt: That's too broad - I've learnt a lot but nowhere near what I need to know to become a fully qualified technician - they are big boots to fill.
As far as hands-on engineering goes, I think other companies that manufacture a different type of goods would be better suited to learn skills. There is a lot of stuff to learn, but in the pharma industry, everything you need to learn about is restricted by validation parameters so you are always extremely limited to what you can do. An automotive manufacturer, for example, is much less restricted on the shop floor and so much more can be done to accommodate learning. I do enjoy it however.
The company itself makes a big deal over its apprentices - monthly meetings are held, trips to other sites, outward bounds activities, getting the parents involved, ect. In that regard they are excellent. However, in the day to day role, the people on the ground are less prepared to accommodate an apprentice and college work can be rushed as we are not given a lot of time to do work on site (some apprentices aren't allowed to do college work at all during their working day). When one assignment normally takes at least 40 hrs to complete, and you get 12 in an academic year (for me that's September to May), social lives and relations at home can be enormously impacted, even obliterated.
Not very. but that can be greatly impacted by how structured my learning provider is; GSK cannot have much to do there. On site, I am given quarterly rotations around the business units and so I see a great deal of site, which is fab, but how time management is structured depends on the manager in that department, and how much individual technicians like having an apprentice in-tow.
Enough to allow me to achieve the best I can, but only if I'm determined to learn, which is fair enough. Sometimes pestering teachers can be a chore and some students cant be bothered with it.
They are very good with general support. When I really need it, GSK provide loads of support, though I normally have to ask for it (how else would they know I need additional support). As far as an employer goes, GSK is fantastic. If I need something, they'll try where they can, whether that's support for learning, mental health, problems at home or other health issues.
Personal living situations means I have it harder than most young people; parents aren't very supportive. But I've never been careless and so have never been in trouble. For a young apprentice, the wage would normally be more than enough. its a good wage as far as apprentice wages go.
Not really for my apprenticeship because its so busy, other apprentices have less to do and have more time for other stuff if they'd like to get involved.
Yes
Because its a good company to work for; they pay well and treat you well.
If I could do it again and chose my own path, I'd start out with an engineering apprenticeship at Nissan, Cummings Engineering, or Hitachi (NE sites that allow for much better training as they are not restricted by validation as much as GSK) and would move to GSK once out of my time because GSK treat you well and have better prospects, and there's engineering, but very clean! - That would be my tip for someone following my path. If I didn't think they would suit GSK, as in they wouldn't like how stringent GSK are, I'd recommend elsewhere.
Details
Higher Level Apprenticeship
Engineering
North East
April 2017