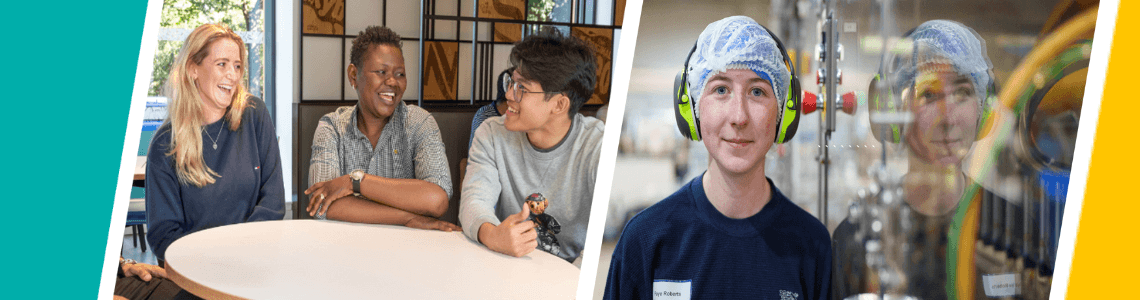
Rating
- 1. Please give an overview of your role and what this involves on a day-to-day basis:
- 2. Have you learnt any new skills or developed existing skills?
- 3. To what extent do you enjoy your programme?
- 4. How valued do you feel by Nestle?
- 5. How well organised/structured is your programme?
- 6a. How much support do you receive from your training provider?
- 6b. How much support do you receive from your employer?
- 7. How well does your salary/package meet your costs?
- 8. Are there many opportunities outside of work?
- 9. Would you recommend Nestle to a friend?
- 9b. Why?
- 10. What tips or advice would you give to others applying to Nestle?
My title at the moment would be J factory operator. However I have been moved off the shop floor for the moment and into the offices in the Quality Department. My daily tasks include doing prep work for the DOR by looking at the all the checks that have been completed on the shop floor and checking for any incident reports that have been raised and to be able to feed this back to the team that are present at the DOR. At the moment I am also heavily involved with a Green Belt problem solving project that is looking at badly wrapped strawberry creams. I have been responsible for the data collection for the project and analysis of the data, and starting to gain an understanding of the programme Minitab. This is all very exciting and I am thoroughly enjoying my time in the quality department and hope to stay here once the project is complete. The quality team are all very friendly and approachable and I look forward to my continued work with them in the future
At the moment I am undertaking the Level 3 Food and Drink Qualification which is completed through block weeks at college where we complete assignments while at the factory to help with this. I am learning more about programmes such as Minitab that are used for data analysis and the systems on Globe that are used to track the checks that have been inputted hourly and any problems that have occured. I am learning more about the quality department in therms of the first off samples that have to be taken and how these are used in sensory sampling, the sensory process and how this is marked on the sheet and the issues that can occur around ineffective cleaning in the factory when product has to go to waste or be reworked. Undertaking a Green Belt problem solving project is obviously hugely imperative in learning new skills and problem solving techniques and the process that has to be followed when undertaking one of these projects; Define, Measure, Analysis, Improve, Control (DMAIC) and I have had the opportunity to present in front of the Future Leadership Team (FLT) which was also very nerve racking but I felt like i improved my confidence and felt less nervous than I thought I would presenting. I have learnt to just ask anyone for help if you need to as everyone is willing to help.
I enjoy the parts of the programme at the minute that get my involved with this problem solving project. I like the independence of collecting the data on my own, analysing it and then trying to present it using graphs and percentages and time series. I feel proud of the work that I am achieving and I think it shows my independence. There are lots of different types of people to interact in within the company, of different backgrounds and cultures and different ranking and its being able to learn to communicate with those of all different aspects of the factory, from the shop worker, to the shift manager, to to the area manager and just being able to understand what they want from the situation. The programme is completely different to what I was expecting...Im not 100% sure what I was expecting but as were were told from the beginning of the programme, its what you make of it. I have the opportunity to go far, as can be seen from those that are in the year above me in positions such as shift coordinator and this inspires me to be able to go far.
When I was part of the Eggs production line I felt like I was a little bit of a spare part as i am not sure they knew what to do with me. I learnt a lot about production but when my manager said that the quality manager had specifically picked me I felt more appreciated and felt like I had an option to put more of my skills from university to use. Now I am part of a team and especially in relation to the Green Belt Project, I really feel valued and that I am contributing to something. My manager has been impressed with my work and I have had good feedback.
I think that the programme has been poorly structured. Induction was spanned over 2 weeks after last year was told that it was not long enough, but feedback from me and from the rest of the year that I started with have said that 1 week would have been sufficient. Everything however at the beginning did seem well structured. Training has been lacking. Initially I was placed on the After 8 line and I got involved straight away with helping and speaking to people on the line and I really enjoyed it, then due to eggs starting up in the end of September/early October time they thought it would be a good idea for me to start then. Most of the line was run by PMP agency staff who has been on the eggs line previously. I was in the quality department along with the 3 others that worked on each of the shifts in quality. I enjoyed picking up knowledge about the quality checks but this soon became quite tedious and due to everyone running the line knowing how to do it, it seemed crazy to have someone train me to work on the machines. I was then put into the production side of eggs where the chocolate is tempered and control over when the plant stops and starts and how fast it runs is all controlled at this end of the plant. This again, was quite exciting to start and then there was talk of me getting signed off on the plant which would involve getting assessed, but this fizzled out and before I knew it, eggs was shutting down for the season. In terms of studying, the time at college was really poor. The first session we had was getting to know the other apprentices from Newcastle and there was plenty of ice breakers which was actually quite good but the work felt unstructured and like the teacher was reading off the board and it was the first time they had read the presentation. However I did learn from things and I think it didnt help that I had covered a lot of this at university. However all in all the first session at college was okay. However the second session that we had in January was not very satisfactory. Again, more new people joined us which was nice to meet and they were all a friendly bunch but the week structure was to look at SOP's and Quality Assurance and Continuous Improvement. Continuous Improvement was the main focus of the week but Quality Assurance and SOP's were not covered which I felt was really disappointing over 5 days of teaching that we did not fit them in where they were in the timetable. The structure was poor and I did not feel like I gained much out of the week. However this was dealt with by the Academy and so far things look like they have been improving, so this is a very positive outcome. Only in the last 3 weeks has there been a mention of a mentor for each of us which is exciting. I just feel overall there should have been a proper timetable and plan in place for us. I realise that it does have its advantages to make it more flexible and make it for us to progress forward but for the first 6 months I think there should have been a set plan with different exposure to different areas and different parts of the factory with little milestones for us to reach and get signed off
At the beginning, as already mentioned this was poor but now that the academy has got involved it appears that this has been rectified a little bit more and if there are any more issues then I feel like [This section of the comment has been removed by a member of the RateMyApprenticeship Team because it did not meet our site terms and conditions] would be a little bit better at helping. Apart from college block weeks however there is not much contact with the college.
There is the support from our apprentice manager and there is support from managers that I have been assigned to but I find it daunting and dont often want to pester my manager when he is running the factory. However, saying that, to this date I have yet to have any major issues and so have no had the need to go to him and I know that if there was something serious wrong that he would be free and make time. Once I have my mentor in place I think this will improve as there will be weekly meetings and easier for me to ask for help and guidance when I need it.
The pay is good and at the moment I have just moved house and bought a car towards the end of last year so I am struggling a little bit with money but the salary is certainly sufficient if this had not been the case.
I am lucky in the sense that I have come here with a life already outside of work with the friends that I made at university and through sports clubs. I dont feel like there is anything to do outside of work and if this was my only social contact then I would struggle. This will probably get better the more settled in I get but at the moment I still do struggle a little bit with the socialising aspect. Volunteering days a couple of days a year is all I know that happens outside of work.
Yes
It is a great company to be a part of and the opportunities are endless if you push yourself. Great variety of people that have come from a variety of backgrounds and I think this great. A really friendly working environment.
The application process is none like I have ever done before. It is based on personality and general fit for the job and so it is questions that you cannot really prepare for which I liked. One of the questions I remember is 'what do you notice first about a person when you meet them'. Things like that you cant prepare for and questions surrounding whether first time right is better than wrong but making a mistake. Makes you think and exposes your rationale towards your way of thinking. The assessment day involved lego building was very interesting and different to everyone just sitting in a room and then interviewed. It made it easier and put everyone at ease- a little bit! They were clear in saying that apprentices play a huge role at Nestle and we have the potential to go far and we are the future of Nestle. I think it would have been nice to know how long it would be before we heard back about whether we had the job. Other than that it was good that we got some feedback after the lego task and then we got to reflect on what we thought we could do better. I also really enjoyed that on the phone we got feedback about what we did well and what we could improve on.
Details
Level 3 Apprenticeship
Yorkshire & The Humber
March 2018