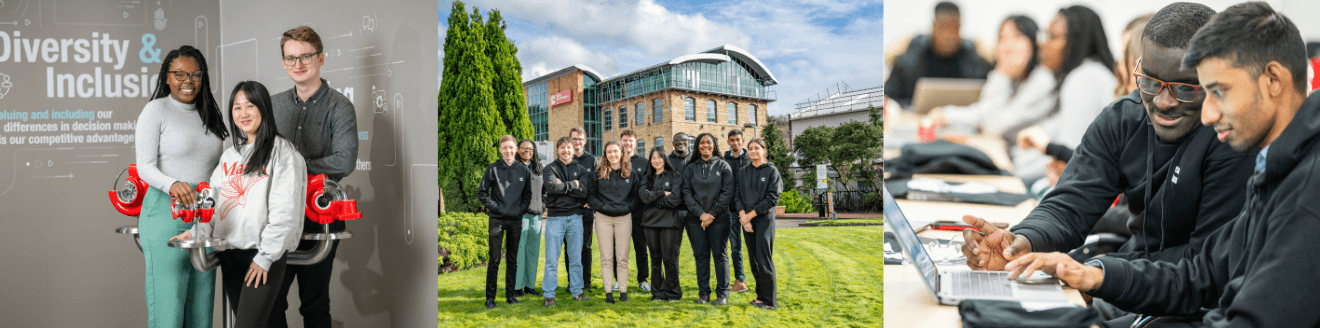
Rating
- 1. Please give an overview of your role and what this involves on a day-to-day basis:
- 2. Have you learnt any new skills or developed existing skills?
- 3. To what extent do you enjoy your programme?
- 4. How well organised/structured is your programme?
- 5. How much support do you receive from your employer?
- 6. How much support do you receive from your training provider when working towards your qualifications?
- 7. How well do you feel that your qualification (through your training provider) helps you to perform better in your role?
- 8. Are there extra-curricular activities to get involved in at your work? (For example, any social activities, sports teams, or even professional networking events.)
- 9a. Would you recommend Cummins to a friend?
- 9b. Why?
- 10. What tips or advice would you give to others applying to Cummins?
The first year of the apprenticeship is spent full-time at Derwentside college, with the academic holidays spent onsite doing short stints in various rotations around DTO. Time at college is split between the workshop and the classroom, doing time in the electrical, welding and mechanical workshop, as well as various theory units towards L3 BTEC including CAD, 3 phase motors and drives, and mechanical principles. The next 3 years are then spent rotating around different departments (currently totaling 14) doing a variety of hands-on work and office work. Depending on the specific jobs apprentices normally start by shadowing a team member, and work their way up to being able to complete jobs on their own with suitable supervision.
While in college workshop skills were introduced or developed, including a lot of time on machines such as lathes and milling machines, as well as welding and electrical. We also spent time learning how to use CAD, starting from the basics, and how to read Engineering Drawings. Since coming onsite I have done both office based and more hands-on rotations, and have developed my skills around tools as well as learning the CAD software used by the company (creo) and how to effectively use software such as Excel and PowerPoint for specific tasks.
The company culture around apprenticeships is brilliant, despite changing rotations regularly you are always made to feel included and a part of whatever team you're on, and everybody is always supportive. The tasks we are given are nearly always interesting learning experiences, and as we change rotations regularly it is rare to do a task so often it gets repetitive.
DTO engineering apprentices spend a full academic year studying at college, and then follow a 3 year rotation plan in Engineering departments around DTO (Darlington Technical Operations - this is the testing and development site) and the plant. We have regular meetings to check everything is progressing well with both Cummins managers and our NVQ assessor from the college.
We have a weekly meeting with our direct manager where we are encouraged to raise any concerns, and a review meeting every other month with various members of the management team where we talk through what we are doing at the time. Our HR rep is easily contactable via teams (or in the office in non-pandemic times), and any issues raised to either her or our manager are resolved as quickly as possible.
Our training provider is Derwentside college, we complete L3 BTEC in yr 1/2, and HNC in yr 3/4, along with L2 NVQ in yr 1 and L3 NVQ in yr 2/3/4. For the first year at college we have a tutor who we can go to with any issues, and classes are taught by a small pool of lecturers. Time in workshops is spent with people who have industry experience. HNC is taught on day release by 1 lecturer who travels to Darlington, who teaches the full course content. We also have a specific person assigned to guide us through completing the documentation for our NVQ3.
The first year at college covers the basics of Engineering, and though our role on site varies it is rare that there isn't something useful that we learnt from college. The fact that we have spent time learning how to understand Engineering drawings and use CAD is probably the most relevant, as most roles require this in some form.
EEEC (Every Employee Every Community) is the company volunteering initiative, and it is strongly encouraged that everybody spends at least 4hrs a year volunteering. This can be completed across a range of tasks to suit your interests/skills. There is an onsite gym, and also a sports and social club which arranges tickets to events. In non-pandemic times most teams participate in team-building activities, and apprentices are invited to join in, and depending on the team we are also invited to Christmas nights out for the department we are in for December and potentially any other department we've been in that year.
Yes
The apprenticeship scheme is very well structured, and there is a very supportive company culture, including some of the global senior engineering positions being filled by people who started their career as a Darlington apprentice. I don't think I've met anybody so far that hasn't encouraged apprentices to ask as many questions as possible.
The interview process is reasonably long, but definitely worth it for a chance to get this apprenticeship which is one of the best in the area. Do a bit of reading up on the company to show you're interested before you get to the interview, but the interviewers are only looking to find the best fit for the role.
Details
Level 3 Apprenticeship
Engineering
Darlington
May 2021