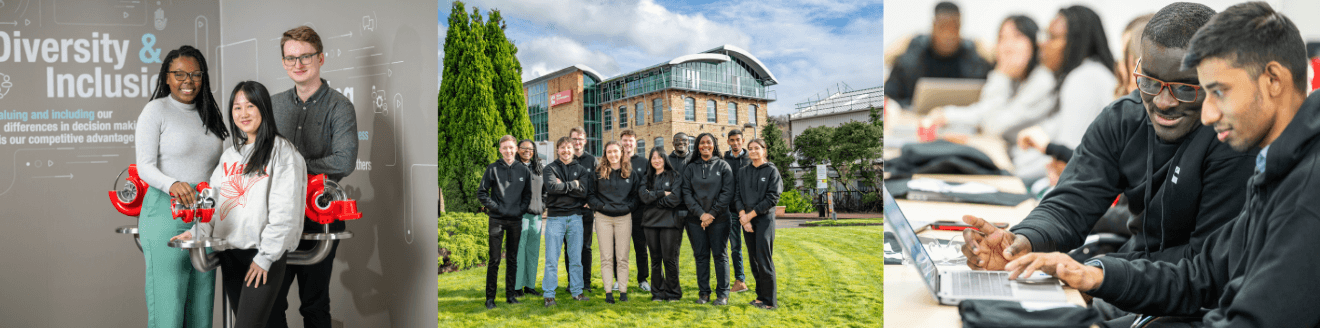
Rating
- 1. Please give an overview of your role and what this involves on a day-to-day basis:
- 2. Have you learnt any new skills or developed existing skills?
- 3. To what extent do you enjoy your programme?
- 4. How well organised/structured is your programme?
- 5. How much support do you receive from your employer?
- 6. How much support do you receive from your training provider when working towards your qualifications?
- 7. How well do you feel that your qualification (through your training provider) helps you to perform better in your role?
- 8. Are there extra-curricular activities to get involved in at your work? (For example, any social activities, sports teams, or even professional networking events.)
- 9a. Would you recommend Cummins to a friend?
- 9b. Why?
- 10. What tips or advice would you give to others applying to Cummins?
At Cummins Inc. I am contracted as an Advanced Technical Engineering Apprentice, under the Darlington Technical Operations facility. Whilst onsite, my apprenticeship is structured around various departments which I rotate within, with the aim of increasing my engineering knowledge. These departments include: Product Engineering, The Pilot Centre, Customer Engineering, Value Package Information Build (VPI), Health and Safety (H&S), Design, The Emissions Solutions, Applied Mechanics, Test Engineering/Technology (Facilities) and the Test Operations (cells) facility. On completion of my programme I am able to decide which department was best suited to me and this is where I will be allowed to fulfil a full time professional career within the company. Whilst in each department I have various tasks to carry out. I am provided with a digital skills matrix to complete, which lists the criteria I must meet in the department and how I've achieved it. It also covers the day to day tasks, training and support for other engineers working in that area. Whilst in product engineering these tasks include, component evaluation and validation, alongside using the theory behind mechanical principles to solve the engineering problems that arise onsite. You must also constantly updating drawings so that they are fit for each individual purpose. You also become involved in change control when revisions to components need to be manufactured. The process is all about making the integration of the new component to come in smoothly and phasing out the old product. When in the Pilot Centre based department, you gain experience with the mechanical and electrical vehicle systems actually installed in the vehicles. You deal with the customers frequently, offering customer support, so you may get to travel to customer sites, so that you meet the specifications to the highest of standards and qualities. This is done by regularly taking measurements of the engine whilst out in the field and ensuring that the conditions of the engine are controlled. When in the Customer Engineering department you must constantly work alongside the customer, looking at the new designs they propose. There are many chances to get involved with international conferences calls and it is your responsibility to look for faults or things that may cause concern in the design of the engine. These comments then get sent back to the customer and they either justify the issue or make alterations to their design so that specifications are met. In the VPI build area, the main day-to-day tasks include working with proto-type engines. Cummins products in this area are constantly built and torn down so that you can take various measurements on the components using a variety of techniques. In this area you also learn how to assemble cylinder heads. In the H&S department it is my job to understand the responsibility and foundations of HSE (the local authority as well as being able to carry out hazard identification in the workplace alongside risk assessments. It is sometimes that you may be given projects to work on in this area too. In the design role, I am able to gain experience with CAD and do various jobs within that department. In the emissions solutions section it is my responsibility to track engineering support software and increase my awareness of mechanical and electrical systems. Whilst in this rotation I will also extend on my knowledge of chemistry and catalyst systems. In Applied Mechanics the job is similar to that of the Pilot Centre in that you are carrying out projects for customers. In Facilities the job consists of programming the engine testing software used in the cells, as well as calibrating the software and measuring conditions on the engine measurement technology. Finally, in the Test Operations department you are based in both the test cells and control room. In here you become involved in engine rigging, running tests on the engines in the cells area, engine installation, engine tear down and rebuild and data analysis of the limits and results the tests provide.
Throughout my apprenticeship I have learnt and acquired a variety of skills. As part of my scheme I am required to attend an engineering training provider. Whilst here I have completed a level 3 BTEC qualification in Engineering, alongside a Performing Engineering Operations qualification (PEO) and am now studying towards a level 4 HNC qualification in General Engineering Mechatronics. The PEO in particular has provided me with new knowledge in Mechanical maintenance, Electrical installation and Computer Aided Design. Although I had knowledge in terms of the theory aspects of Electrical appliances and circuit components from A level of physics, I have been able to extend on the theoretical sides and actually apply the theory to practice. I hadn't much experience in terms of the Mechanical maintenance tasks which I learnt to carry out on the milling machine. These included, assembling and disassembling the feed drive gear box, speed selector gear box and the coolant and lubrication pump. Likewise I have had no experience with CAD and so this aspect of the job was a completely new skill that I have had the chance to have exposure to. Alongside this I have also been provided with additional skills training. This included gaining experience in the fabrication and welding section. Here I learnt how to use industrial machinery such as guillotines, bench knifes, folding machines and hydraulic presses- all of which were used to design things such as a tool box, cylindrical log burner and a tie fighter stove. I also had chance to have a look at different joining techniques in Metal Inert Gas welding, including lap, fillet and corner joints. I also spent time in the tool making section in the additional skills course which includes milling and turning. I had not had any experience with any pieces of these equipment and so have learnt how to operate them safely as well as knowing what different parts of the machine are called and do, such as: the knee, the spindle, the feed table, the quill, the drawbar, the head, the base, the column, the reservoir etc. More specific to the job, I have learnt about various components of the engine and how an engine works. Although interested in engines before, I was unaware of this knowledge and so have learnt something else new.
I am currently enjoying my programme every day. Admittedly, at first and still sometimes now to a certain degree I am apprehensive, given that I lacked engineering experience prior to joining Cummins. However, I am learning all the time as previously mentioned and becoming more confident each day. The apprentices who I am on the programme with have become really good friends of mine and the dynamics of the group makes it a pleasurable experience on a daily basis. I enjoy being part of such a successful global power leader and the company itself in terms of their treatment of employees makes it an honour to work for. The Company aim and achieve their duty of care and inclusion with all diverse groups of people and it is the community and atmosphere across the site that makes the experience even more enjoyable. To this present day the apprenticeship programme has met, if not exceeded my expectations. This is because I am becoming more competent with practical tasks which I have had no prior experience in.
The programme to date has showed evidence that it is very well structured. It began with a informative induction covering the corporate policies, code of conduct, how we would spend our time and the health and safety on site. We have received a rotation plan in the spread sheet format informing us which departments we are in and at what time. It also informs us of the duration of that rotation and who you must report to. There are various opportunities to flag concerns as the company has made it mandatory that there is a weekly apprentice meeting. However, alongside this Cummins work by having bi-monthly appraisals/reviews with managers and the leadership team. This looks at how you are progressing and coping with life as an apprentice and gives you an opportunity to ask any questions or for support. The company has provided us will laptops so that we are able to contact them both on and offsite and most managers are very quick in their response to help answer any queries. In each department you are assigned with someone who acts as your mentor and work buddy, so they are at your disposal the majority of the time which is very beneficial. As previously stipulated we are provided with matrix sheets which cover what criteria we must and are expected to meet. This offers a guidance of how to conduct your day-today tasks and is helpful in terms of its structure as it can be used as a check-list essentially.
My employer is extremely helpful in terms of the support they offer. In the bi-monthly reviews, if you flag up a concern about a certain topic or department, they can assign you to specialist individuals, with in-depth knowledge in that area or subject which will help you through your concerns. Likewise, as previously covered, the company provided us with laptops so that we have easy access to all members off staff and the management team. I've had members of the management team who have told me not to hesitate contacting them. Even if they don't initially know the answer, they have told me that they will do their own independent research and dig out resources they have at their disposal to try and assist myself. This is in addition to the weekly scheduled meetings they arrange for all apprentices to discuss their general progression in our departments and educational studies.
During the course of my apprenticeship our training provider transferred from South West Durham Training to Derwentside College. Although I have learnt a variety of new skills from my training provider there are a few minor issues. It is often that the HNC lecturing structure could be improved. It is commonly observed that the tutor has a tendency to over complicate subject topics and sometimes go off on tangents which is not beneficial. With regards to the NVQ qualification there have been several changes in staffing in terms of the responsible assessor coordinating this. This has lead to unclear direction and limited support, hopefully this will be addressed once the new job holder is in position. The standard of qualification we're on for the NVQ is new to the education sector, which has felt like they themselves lack knowledge on what the expectations are and for preparing us sufficiently.
The HNC is very effective in your performance within an apprentice role, as it educates you on the fundamentals of thermodynamics, which we are exposed to within the testing environment. This helps us to understand the theory and techniques used to monitor the engine and means we can apply it to real working life tasks. It helps us to understand the relationships between different forms of energy’s being used within the process. The qualification is also beneficial as it teaches you how to sufficiently document, conduct and log coherently, a project you have been assigned, relative to the business. This helps with the planning and approach to finishing projects assigned by our manager. Likewise, the HNC can probe you to think creatively through the use of its engineering design module, which coincides with how Cummins products and processes are constantly evolved. As a Technical Engineer apprentice, we are exposed to both mechanical and electrical technologies and equipment – we must be multi-skilled. The HNC has two units which cover both elements in detail, which is therefore very effective as it ensures that you understand the theoretical principles of both disciplines and how they function. All engineers are renowned for using quantities and numerical values, calculations are made all the time when testing, design and validating engines. The HNC is heavily mathematically based, which is obviously essential in an engineer’s role, to understand how to derive equations and calculations which we can then base ideas off or generate conclusions from, to make our product more reliable and efficient.
There are many opportunities for involvement outside of working hours. Cummins offer leisure facilities such as the gym onsite. This is £10 a month for access but they offer a reduced deal where you can pay £8.50 a month by joining the leisure club and facilities full package. Cummins care about the community and so make it mandatory for every employee to conduct a minimum of 4 hours charity or voluntary work each annual year. It is therefore that they hold many events to meet this criteria. Examples of this included going into schools with younger pupils and helping them build small powered go-karts. The result was that they went up to Nissan at a later date to test drive and race them. Furthermore Cummins host and attend informative careers days at various locations, emphasising the benefits an apprenticeship can offer. In addition to this, when you rotate around the departments, individuals organise team bonding exercises outside of work, whether that be playing sport or just generally socialising. Cummins have a sports and social clubs which communicates upcoming various events that you can participate in.
Yes
Cummins is a global power lead based in more than 190 countries, making it a very successful distributor, manufacturer and supplier of diesel engines. Working for such a company has given me an invaluable opportunity to work with professionals within Cummins Engines. They are a leading edge organisation which are producing innovative and new technology at all times. This makes all aspects of the job significantly interesting. Being part of a global company is truly rewarding, both for the personal benefits they provide you with and how you supply a product that many people rely on and has shaped our world today. Cummins are a very caring company and look after all employees thoroughly and it is this reason I cannot emphasise how much I recommend them as an employer.
The main advice I would give would be to do sincere and in-depth research before applying. This includes constructing your CV and covering letter around what Cummins are looking for, in terms of desired qualities - but be truthful and provide evidence that you do offer these particular qualities. I would also advise that you prepare significantly for the interviews. Research frequently asked questions and think of competency based examples. You should also do a thorough background check and research on the company so that they are aware you are properly engaged and interested with what they do. In addition to this on assessment days I would encourage that you try to get involved to a good extent, but don't become too over powering. It's important that you listen to others and take on board their opinion and suggestions in relation to the task. Furthermore its good to show that you try to involve everyone in the group and aim to engage the more quiet people into the group and task. This same process applies to the onboading process, apart from that you make notes and show a great interest in the history of Cummins, which you learn about.
Details
Level 3 Apprenticeship
Engineering
Darlington
May 2021