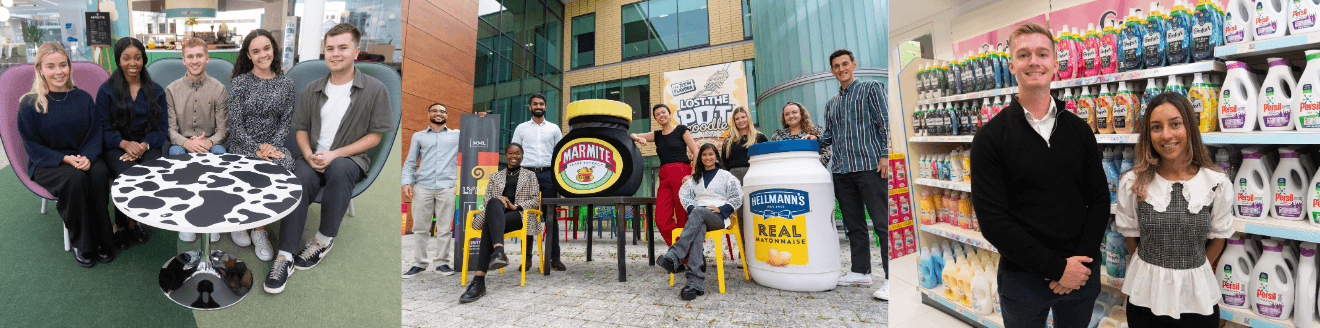
Rating
- 1. Please give an overview of your role and what this involves on a day-to-day basis:
- 2. Have you learnt any new skills or developed existing skills?
- 3. To what extent do you enjoy your programme?
- 4. How well organised/structured is your programme?
- 5. How much support do you receive from your employer?
- 6. How much support do you receive from your training provider when working towards your qualifications?
- 7. How well do you feel that your qualification (through your training provider) helps you to perform better in your role?
- 8. Are there extra-curricular activities to get involved in at your work? (For example, any social activities, sports teams, or even professional networking events.)
- 9a. Would you recommend Unilever to a friend?
- 9b. Why?
- 10. What tips or advice would you give to others applying to Unilever?
Throughout the apprenticeship, I have moved between the various departments in my factory to build my skill in each area. It involves learning the new machinery; carrying out maintenance activities; working with the other engineers on site; contacting external suppliers and contractors; participating in meetings; leading and progressing improvement projects; being trained in new technologies and machinery. As it is an apprenticeship, I am also currently at college 1 day per week completing a HNC qualification. Tasks change day-to-day, however it generally consists of maintaining machinery or fixing them when they break down.
Throughout the apprenticeship, I have learnt various new skills relating to the engineering industry. I was taught a lot of theory about the different aspects that the role will entail. In college we were taught how to use workshop equipment such as lathes, milling machines, various types of welding (TIG, MIG, STICK), using a plasma cutter; as well as bench fitting techniques using various hand tools. On site I am then taught about all departments on site and what they entail - including learning about compliance, pneumatics, hydraulics, health and safety, quality, mechanical and electrical systems, PLCs, AC units, etc. Lots of interpersonal skills are also developed through communicating with colleagues of all ages, participating in meetings, leading projects, communicating with external suppliers. Any skill I had at the start of the apprenticeship has been further developed through completing this apprenticeship.
I really enjoy the program as it has taught me a lot about the engineering industry, and what consists of being an engineer. Being taught how to operate lathes and milling machines was very enjoyable, with a lot of the theory about how machinery and engineering concepts work being very interesting. Through working in every department in the factory, I have been able to increase my skills in other aspects as well as engineering, such as health and safety, quality, manufacturing - having this variety has made it more interesting, being able to discover each aspect within the industry.
For me the programme was very well structured throughout the entire course. The first year was spent at college learning the basics about engineering, as well as practical skills within the workshop. During this year I finished an NVQ level 2 and first year of BTEC qualificiations. The second year was block release at the same college, spending time completing the rest of my BTEC qualification. This was further learning about the theory side of engineering. During this point, my apprenticeship was changed from a 4 year programme to 5 years. For this reason, year 3 was a 'gap year' during which I was based in the factory full time completing my NVQ level 3. Years 4 and 5 are then a mixture of block and day release while completing the HNC level 5 qualification. While on site, it was organised that I would spend around 9 months in each department to learn about what it entailed. There were also numerous mentors in each department to help my progression. and who I could approach for more training or if I was in need of support. The programme has not been as well organised as previous years due to Covid, and so I have missed out on some extra training (such as Siemens) that previous apprentices took part in.
Whenever I am in need of support, I am able to reach out to anyone within my factory who are always very helpful. When trying to approach the apprenticeship lead role who is external of my site, it was not always easy to get in touch or receive a great amount of support. The on site team however constantly and continue to support me whenever I need it.
I receive a lot of support from my training provider whenever asked - however it has not always been easy due to Covid and working from home for a year. That being said, all messages and emails have always been answered in a timely fashion, with any questions being answered. During the second year there were several issue relating to lecturers and timetable issues, and so there was some what a lack of support during this period. However, there have been no issues since this time.
My training provider has taught me a lot of theory relating to my day-to-day job within the factory. There are various aspects that I have been able to do better within my role thanks to learning about them within college. There are however a lot of subjects that I am not directly using withing my role - they do however make me a more rounded engineer, providing me with knowledge that I may use at some point in the future either in a different role or different factory. The training in the workshop has massively helped me to perform practical bench fitting tasks, which I use most days. As some of the qualification requires a project to be planned and carried out, it has also helped me to perform similar tasks in my role to a high standard. The only aspect I feel would have helped further is if I learned more about electrical systems - though this is more due to my employer choosing different units to study within the programme.
During the apprenticeship, there were several outward bound events that we could take part in. These helped to build confidence and get to know the other apprentice within the course. There was also a large networking event for all Unilever apprentices at their headquarters in Leatherhead. Various seniors management employees were also present while we conducted various tasks and team building exercises. We can also communicate with our CEO on regular occasions as they carry out presentations regarding the company, talking about any updates and the current performance overall. The whole company are invited to virtually participate in the meeting, also being able to ask any questions that they would like the CEO to answer.
Yes
It is a successful blue chip company, and has various different career paths that you can follow. They are very supportive in progressing from within, and have a variety of roles that you can progress into - including engineering, manufacturing, HR, projects, IT, business, etc. They also work in various different sectors and industries that you can work in and move across to internally, such as ice cream, food and beverages, personal care, etc. They also offer lots of benefits to being an employee, such as a annual bonuses and pay rises, 'Unilever discount' which provides offers and discounts on named brands, staff shops that sell Unilever products at a discounted rate, BUPA, pension scheme, share buy scheme, etc.
Look into what Unilever as a company stands for, and work towards the same goal - this includes them progressing to become a more sustainable company, helping the environment and enhancing the livelihoods of others. Unilever look for people who share the same outlook to employ. In terms of engineering, the assessment days consist of practical tests - so you need somewhat basic skills before applying. You are marked on how you approach each task, and how well you have met the criteria. There is also a group exercise with others that have applied - during this task, make sure you take part and try to lead it if you can. Just communicate a lot, try to delegate where you can, listen to others ideas, compromise in some areas. Make sure your actually being helpful and working as a team. In the interviews, for an engineering role they would like a project to show during the interview. If you have done something like that in high school/college, bring that in with you. Make sure you try to talk about aspects like health and safety, working to a brief, communication, etc. Try to get some work experience similar to this field before applying - you should then pick up some terminology to use during the interview. Don't rush anything, take your time - they would rather you do something safely and get it correct. Try to relax, they are also trying to see if you would be a good fit for the team - if you get along with everyone and can communicate well.
Details
Higher Level Apprenticeship
Engineering
Manchester
May 2022