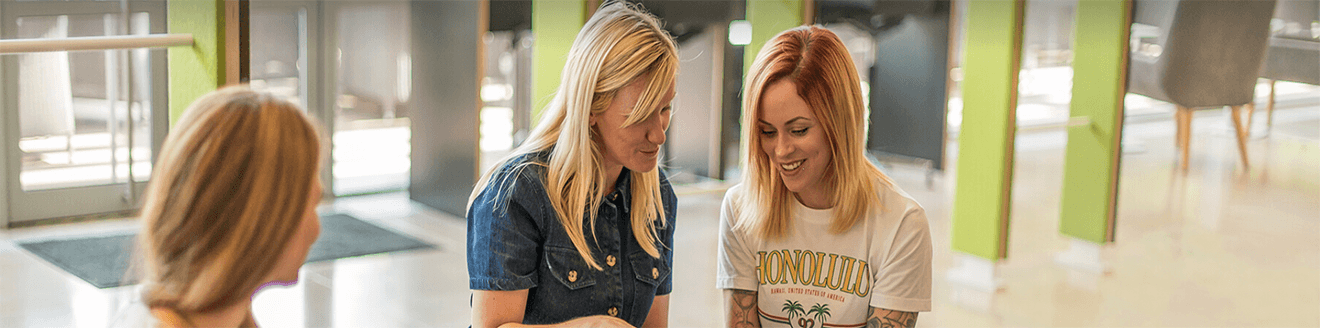
Rating
- 1. Please give an overview of your role and what this involves on a day-to-day basis:
- 2. Have you learnt any new skills or developed existing skills?
- 3. To what extent do you enjoy your programme?
- 4. How well organised/structured is your programme?
- 5. How much support do you receive from your employer?
- 6. How much support do you receive from your training provider when working towards your qualifications?
- 7. How well do you feel that your qualification (through your training provider) helps you to perform better in your role?
- 8. Are there extra-curricular activities to get involved in at your work? (For example, any social activities, sports teams, or even professional networking events.)
- 9a. Would you recommend AstraZeneca to a friend?
- 9b. Why?
- 10. What tips or advice would you give to others applying to AstraZeneca?
As a manufacturing technician over the 2 years I am involved in multiple aspects of the manufacturing process. Currently I am working with the manufacturing executive systems team where I have taken on 2 projects. These are both digitisation focused and involve communicating and planning with colleagues to deliver a smooth transition in my workplace from analogue to digital practices. In the past I learnt how to run a packing line and be a part of a packing team but now I spend time both on and off plant viewing different areas that fall subject to my projects and organising the progression of the projects.
I have learnt how to comply to good manufacturing practice and health and safety regulations that are involved in the production of pharmaceutical products. This includes proper dress code for white areas and knowledge of the procedure required to entire a sterile area. I have developed my IT skills by spending time training to use Excel, Power apps and Adobe Sign to aid my projects. I have also learnt a lot about manual handling and procedural tasks within a warehouse and packing line environment.
I thoroughly enjoy my current placement in my apprenticeship. In previous placements I have felt as though I was not learning as much as I'd like to or not receiving any priority to being trained in the area I was working. However, since my move to the MES team I am again happy with my progression of knowledge about the business and how many of the manufacturing processes work.
My programme has structure but it is not rigid. There have been periods of time where I was left asking about future placements as an area I was working in was sold as a product and so I didn't continue to work there. Instead I spent 3 months in a temporary placement where I received minimal training as colleagues were unsure as to how long I was staying with them for. Since speaking to past apprentices I have learnt that there is no set rota that you do as a manufacturing apprentice and that the placements that you do vary depending on where you can be fit into the business. This results in some apprentices finishing with more work based validations/training that others for example a sterile license to work in a sterile environment.
I receive a good amount of support from my employer when I ask for it but I typically do not require much support. When I have struggled in my apprenticeship I have had appropriate support but still didn't feel as though it was proving to be much of a benefit. Despite this I feel much better about my level of support now as I have a manager of my team that regularly checks in with my current work load.
There is a small amount of support available from my training provider to me. Support I have received has been extended deadlines, the provision of materials we are working from and offers of spending time out of hours to catch up at the college itself which has given me the opportunity to catch up on my college work at times. I do feel as though my current position at college is owed to myself working outside of hours at home to catch up though.
I do not feel as though there is much correlation between my qualification and my role. The only crossover I have experienced has been in the health and safety aspect of the course as during this time I was working in the warehouse environment at work. Although the college course definitely has valuable aspects to it in terms of engineering knowledge, much of it is self taught through research and does not feel entirely specialised.
The apprentice society has many events available to attend that are open to apprentices across site. For the majority of my time spent working at AstraZeneca I have been working a shift pattern meaning it was not appropriate for me to attend these. Now that I am working a similar shift to the rest of the apprentices now, I can attend these events more frequently. Outside of these social events, various teams I have been a part of have had extra-curricular events that I have been involved in such as football teams and volunteering days.
Yes
I feel as though the working environment here at AstraZeneca is fantastic. The attitude that employees have towards each other and the company demonstrates the signs of a very healthy workforce. Aside from this, I have thoroughly enjoyed my own learning experiences here in my workplace and the access to information I have about everything manufacturing. Being able to ask questions and learn about different processes as well as the future possibilities that someone could have in a career here is what makes this job so exciting to me and one of the reasons I'd recommend it to a friend.
Demonstrate your strengths as a character and learn how to put yourself across to others in a good manner. Be professional and approachable in your interviews and make the application process a priority of yours as the pay off is an extraordinary opportunity to take your first steps into the world of pharmaceutical manufacturing.
Details
Level 3 Apprenticeship
Science
Macclesfield
January 2023