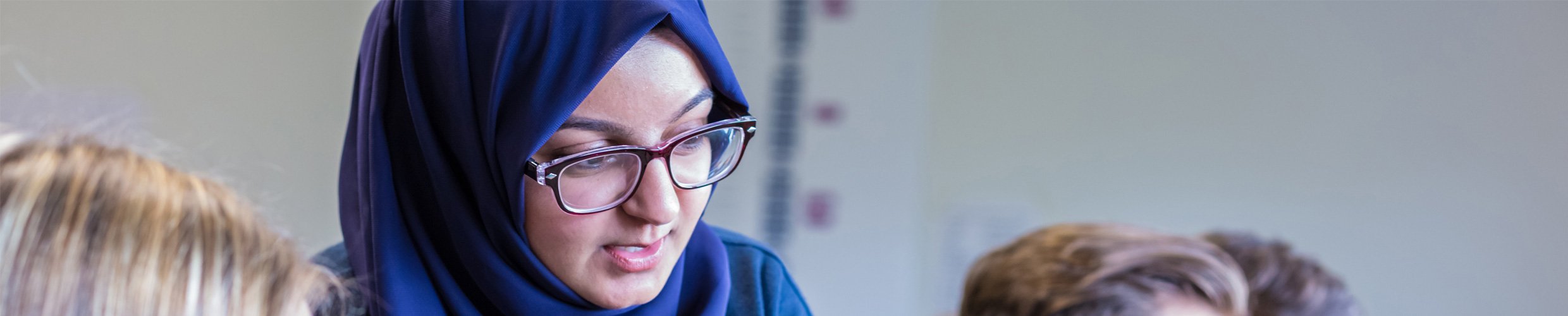
Rating
- 1. Please give an overview of your role and what this involves on a day-to-day basis:
- 2. Have you learnt any new skills or developed existing skills?
- 3. To what extent do you enjoy your programme?
- 4. How well organised/structured is your programme?
- 5. How much support do you receive from your employer?
- 6. How much support do you receive from your training provider when working towards your qualifications?
- 7. How well do you feel that your qualification (through your training provider) helps you to perform better in your role?
- 8. Are there extra-curricular activities to get involved in at your work? (For example, any social activities, sports teams, or even professional networking events.)
- 9a. Would you recommend Rolls-Royce to a friend?
- 9b. Why?
- 10. What tips or advice would you give to others applying to Rolls-Royce?
I am training to be an engine fitter with main duties including assembly and disassembly of turbofan modules and components. My training is split between practical business placements and college learning. I am not aligned to any specific area of the business and have completed placements in production, experimentals, and engine overhaul services.
I have learned many new practical skills while undertaking the apprenticeship such as fitting techniques, electronics, tool use, inspection etc. While my practical skills have improved, I have not had as much time on the tools as I would like due to a combination of COVID and poor organisation of placements.
I enjoyed the first year of my programme as it had a good structure and clearly laid out what we had to learn and how we would be learning it. Beyond this I have had little enjoyment of the programme overall after having spent almost 3 and a half years with the company.
The programme is organised very poorly. After the first year, apprentices are unleashed into the business without any plan or explanation of what they are training towards and essentially left to sink or swim. Business placements are organised at the last minute and do not always provide the jobs needed to acquire NVQ evidence, although this has improved somewhat.
Apprentices are assigned an ADL and NVQ assessor. Neither of them are present on the shop floor thus support for day to day activities is limited. The level 3 NVQ rollout is not explained to apprentices, with no help given on how to gain evidence, which is crucial to completing the apprenticeship. EPA is similar, with apprentices left to work their way through it and find what they need by themselves. Documents and processes that would be helpful are not passed on by the apprentice support team and are instead stumbled across at random by apprentices and shared amongst peers.
Our training provider provides assessors that often have no engineering experience, thus any support they give is limited to the minutia of the NVQ process and not on actually gaining evidence from specific jobs on the shop floor. There are not enough assessors thus the amount of time any one apprentice is afforded with their assessor is limited to monthly reviews.
The qualification itself is sound. The training, support, and organisation to deliver the qualification is not. The practical NVQ qualification is useful for gaining practical skills needed for the job, although some specific jobs are out of date and should be reduced from the criteria. The college side of it is interesting and does provide a wider understanding of the product, but is poorly delivered by the college.
There is an apprentice-graduate association that organises extracurricular activities but is somewhat irregular and seems to be entirely populated by graduate apprentices with very little representation from other apprentice groups. There are also stem events which can vary widely but can be useful for improving communication skills and networking outside the company.
No
Rolls-Royce rely on their reputation for excellence to draw people and customers but it is a lie. They have world class products but do not have world class processes. The management are completely intransigent - issues that are raised by workers and apprentices alike are routinely ignored, sometimes for years. The management are very skilled at making it look like they are addressing problems without actually putting in effort to fix anything. We are taught lean manufacturing principles yet the company does not practice what it preaches. It is no mystery why the company is struggling.
Ask yourself if the programme is delivering the qualification you really need and if it is search to see if there are other providers available. It is entirely possible to complete an apprenticeship with this company, but you will not be given the support you need and you will essentially be running the programme yourself.
Details
Level 3 Apprenticeship
Engineering
Derby
February 2023