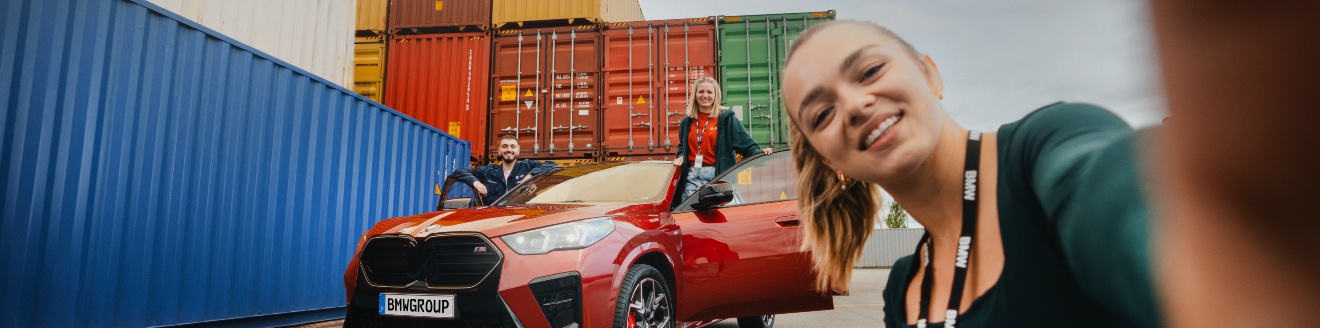
Rating
- 1. Please give an overview of your role and what this involves on a day-to-day basis:
- 2. Have you learnt any new skills or developed existing skills?
- 3. To what extent do you enjoy your programme?
- 4. How well organised/structured is your programme?
- 5. How much support do you receive from your employer?
- 6. How much support do you receive from your training provider when working towards your qualifications?
- 7. How well do you feel that your qualification (through your training provider) helps you to perform better in your role?
- 8. Are there extra-curricular activities to get involved in at your work? (For example, any social activities, sports teams, or even professional networking events.)
- 9a. Would you recommend BMW Group to a friend?
- 9b. Why?
- 10. What tips or advice would you give to others applying to BMW Group?
The apprenticeship consists of completing 3 month placements in various departments across the business. In the engineering related functions, often department roles are split according to parts of the car. Typical activities in the placements include shadowing people in the departments to learn more about their role, learning how the cars are built on the line, assisting with vehicle checks and test drives, making measurements on parts of the car.
I have learned how to comply with the company's safety requirements, use CAD, and measuring equipment such as robots and specialised software to complete investigations on components and assemblies on vehicles on and off the assembly line, and how to read and interpret the information found in the bill of materials.
Overall, I mostly enjoy the apprenticeship but this is strongly influenced by how active the department is and how much responsibility I am given. Some employees are more willing to involve an apprentice in their work, whilst others barely acknowledge you are there, which sometimes discourages apprentices from asking to get involved with more challenging work. I have enjoyed getting involved in various activities in the Plant and externally at suppliers and at test tracks.
In our first year we are based in the Training School 5 days a week. From the second year onwards, 4 days a week are spent in our work placements and 1 day a week we are in the Training School for college/university. The work-based side is pretty well structured. There is a placement plan but this sometimes changes, so it can be difficult to know how our placements link with our final role. In the placements so far, the targets have been vague, which makes it difficult to gauge which tasks we should be completing to improve our ability. Unfortunately in placement when there are quieter periods, or if the employees spend a lot of time working from home, I sometimes end up with little work/learning opportunities despite repeatedly asking around and volunteering to help. This can be demotivating. On the other hand, the college side is poorly structured. Most days we go to class to find out that our tutor is absent or late, and this year in particular there has been a lot of confusion over the units being covered and the assessment requirements (rushed and inadequate exam preparation).
The company is extremely supportive, and the managers are very understanding if we need to complete university work or if there are personal situations outside of work that are affecting us. However, it is extremely difficult to get the training required for our future job roles. For example, some of us have not received high voltage electrical safety training, which is mandatory for working safely on or near electrical vehicles. This has been raised numerous times by the apprentices and placement managers but no progress has been made. This is disappointing, as we are not being appropriately prepared for our future job roles, and could get in trouble for being in an unsafe environment, doing work we are not permitted to do.
Very little support has been provided by the college over the course of the apprenticeship, and the little positive support has been extremely rushed and has arrived too late to have an impact on our learning. We spend our 1 day a week at university in the classroom for the whole day and there is no practical element to our curriculum, despite the course specification stating that the time must be split between the classroom, and in specialist spaces such as workshops, laboratories and potentially seeing the application of course topics in the workplace or on external visits. Sitting in front of a screen for almost 10 hours with little engagement between the tutor and the whole class is extremely draining and can cause students to lose concentration and enthusiasm for the lessons. This feeling is aggravated by the poor delivery of lessons. At the start of the apprenticeship we also did not have access to the university online library for resources to complete the independent research required for assignments, which meant that we had to find resources on Google and YouTube. Often we are given assignments that had been set for the other class of Engineering Technicians in other plants with no updates made to the assignment brief (sometimes other students' names remain on the student assigned data sheet for mathematical calculations). There is no transparency about the progress being made by other Engineering Technicians working in the other plants and how they feel about their course.
The practical learning in the first year (electronics, electrical, PLCs, hand fitting, turning and milling) can be useful for university projects and occasional tasks given to us in our placements. However, very little of the qualification is useful for my role. At the moment, only knowledge gained from the CAD and Quality Systems units have been used in my day-to-day job. Our ability to apply knowledge gained from the course to our jobs has been severely limited by the way the units have been delivered (only assignment questions are covered with no other contextual knowledge).
There is an Apprentice Newsletter team as well as Charity Champions, Apprentice SharePoint Team and Apprentice Network meetings to get involved with. When going to placements you may learn that there are some sports teams and department socials organised outside of work, but not many sports or hobby activities for apprentices. If you are not originally from Oxford or the local area it might be difficult to know what to visit/do in your spare time when you first arrive. There have been little opportunities to discover the other Plants.
Yes
Working at BMW Group gives you the opportunity to work in world-class manufacturing and testing facilities, as well as expanding your network and knowledge about the Automotive and Manufacturing industries. It also gives you the opportunity to gain work experience and a qualification without incurring debt and being able to live independently. You also have the opportunity to visit interesting process partner sites and test facilities.
Show you are interested in the industry and the facilities available in the Plant and reach out to try to get some work experience within the company or industry. Try to promote the potential you have to the hiring managers by showcasing the skills you have gained in school, projects and in your career.
Details
Degree Apprenticeship
Automotive Engineering
Oxford
April 2024